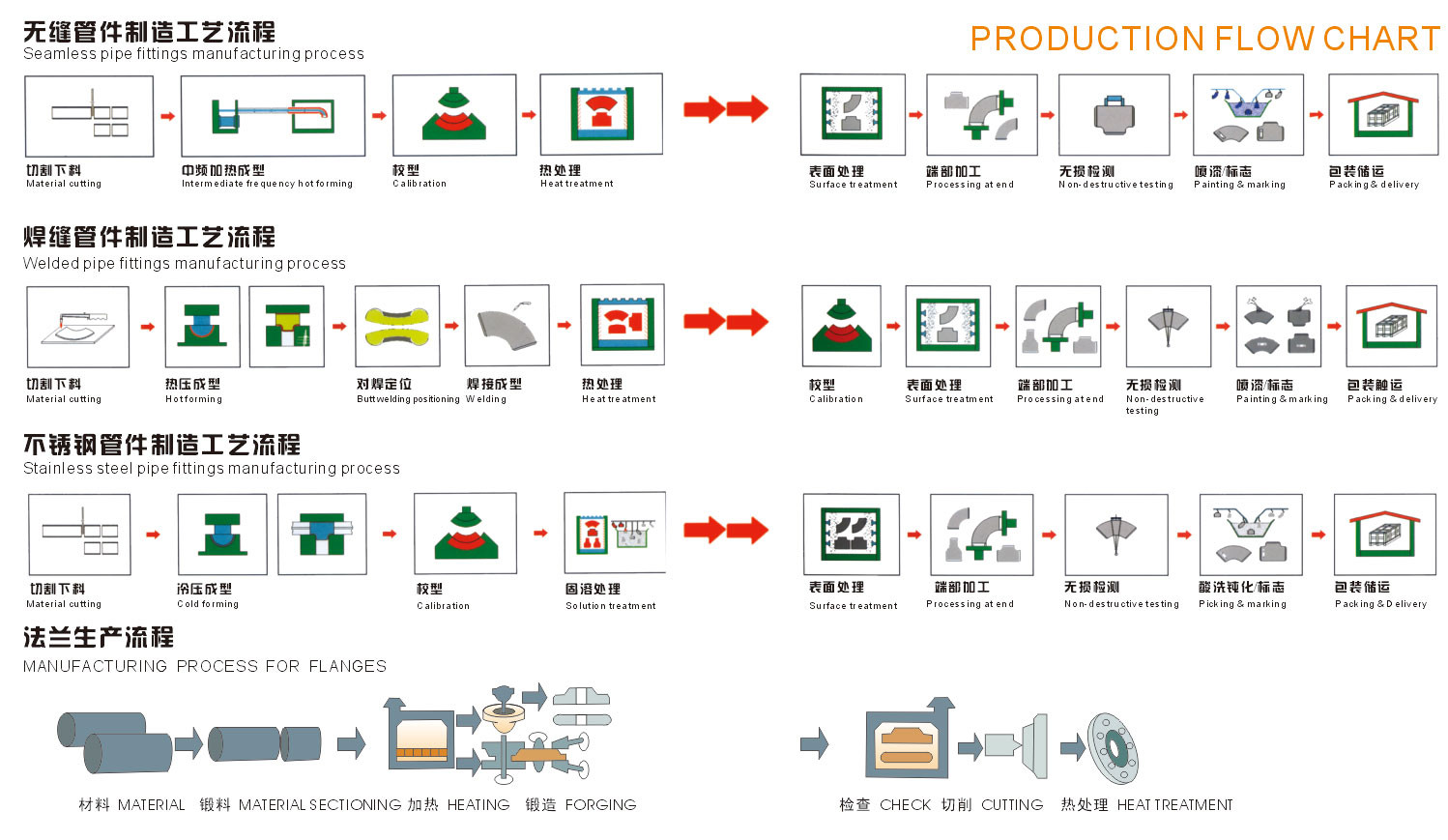
1. Material
1.1. The selection of materials shall comply with the relevant standards of the pipe producing country and the raw material standards required by the owner.
1.2. After entering the factory, the inspectors first verify the original material certificate issued by the manufacturer and the material commodity inspection report of the importer. Check whether the marks on the materials are complete and consistent with the quality certificate.
1.3. Recheck the newly purchased materials, strictly inspect the chemical composition, length, wall thickness, outer diameter (inner diameter) and surface quality of the materials according to the standard requirements, and record the batch number and pipe number of the materials. Unqualified materials are not allowed to be warehoused and processed. The internal and external surfaces of the steel pipe shall be free of cracks, folds, rolling folds, scabs, delaminations and hair lines. These defects shall be completely removed. The removal depth shall not exceed the negative deviation of the nominal wall thickness, and the actual wall thickness at the cleaning place shall not be less than the minimum allowable wall thickness. On the inner and outer surface of the steel pipe, the allowable defect size shall not exceed the relevant provisions in the corresponding standards, otherwise it shall be rejected. The oxide scale on the inner and outer surfaces of steel pipes shall be removed and treated with anti-corrosion treatment. The anti-corrosion treatment shall not affect the visual inspection and can be removed.
1.4. Mechanical properties
The mechanical properties shall meet the standards respectively, and the chemical composition, geometric dimension, appearance and mechanical properties shall be rechecked and accepted.
1.5 Process performance
1.5.1. Steel pipes shall be subject to 100% ultrasonic nondestructive testing one by one according to SEP1915, and standard samples for ultrasonic testing shall be provided. The defect depth of standard samples shall be 5% of the wall thickness, and the maximum shall not exceed 1.5mm.
1.5.2. The steel pipe shall be subject to flattening test
1.5.3. Actual grain size
The actual grain size of the finished pipe shall not be thicker than grade 4, and the grade difference of the steel pipe of the same heat number shall not exceed grade 2. The grain size shall be inspected according to ASTM E112.
2. Cutting and blanking
2.1. Before blanking of alloy pipe fittings, accurate material calculation shall be carried out first. According to the strength calculation results of pipe fittings, analyze and consider the influence of many factors such as thinning and deformation of pipe fittings in the production process on the key parts of pipe fittings (such as the outer arc of elbow, the thickness of tee shoulder, etc.), and select materials with sufficient allowance, And consider whether the stress enhancement coefficient after pipe fitting forming conforms to the design stress coefficient of the pipeline and the flow area of the pipeline. The radial material compensation and shoulder material compensation during the pressing process shall be calculated for the hot pressed tee.
2.2. For alloy pipe materials, the gantry band saw cutting machine is used for cold cutting. For other materials, flame cutting is generally avoided, but band saw cutting is used to prevent defects such as hardening layer or crack caused by improper operation.
2.3. According to the design requirements, when cutting and blanking, the outer diameter, wall thickness, material, pipe number, furnace batch number and pipe fitting blank flow number of raw materials shall be marked and transplanted, and the identification shall be in the form of low stress steel seal and paint spraying. And record the operation contents on the production process flow card.
2.4. After blanking the first piece, the operator shall conduct self inspection and report to the special inspector of the testing center for special inspection. After passing the inspection, blanking of other pieces shall be carried out, and each piece shall be tested and recorded.
3. Hot pressing (pushing) molding
3.1. The hot pressing process of pipe fittings (especially TEE) is an important process, and the blank can be heated by oil heating furnace. Before heating the blank, first clean the chip angle, oil, rust, copper, aluminum and other low melting point metals on the surface of the blank tube with tools such as hammer and grinding wheel. Check whether the blank identification meets the design requirements.
3.2. Clean up the sundries in the heating furnace hall, and check whether the heating furnace circuit, oil circuit, trolley and temperature measurement system are normal and whether the oil is sufficient.
3.3. Place the blank in the heating furnace for heating. Use refractory bricks to isolate the workpiece from the furnace platform in the furnace. Strictly control the heating speed of 150 ℃ / hour according to different materials. When heating to 30-50 ℃ above AC3, the insulation shall be more than 1 hour. In the process of heating and heat preservation, digital display or infrared thermometer shall be used to monitor and adjust at any time.
3.4. When the blank is heated to the specified temperature, it is discharged from the furnace for pressing. The pressing is completed with a 2500 ton press and pipe fitting die. During pressing, the temperature of the workpiece during pressing is measured with an infrared thermometer, and the temperature is not less than 850 ℃. When the workpiece cannot meet the requirements at one time and the temperature is too low, the workpiece is returned to the furnace for reheating and heat preservation before pressing.
3.5. The hot forming of the product fully considers the law of metal flow of thermoplastic deformation in the forming process of the finished product. The formed mold tries to reduce the deformation resistance caused by the hot processing of the workpiece, and the pressed tire molds are in good condition. The tire molds are verified regularly according to the requirements of ISO9000 quality assurance system, so as to control the amount of thermoplastic deformation of the material, so that the actual wall thickness of any point on the pipe fitting is greater than the minimum wall thickness of the connected straight pipe.
3.6. For large-diameter elbow, medium frequency heating push molding is adopted, and tw1600 extra large Elbow push machine is selected as the push equipment. In the pushing process, the heating temperature of the workpiece is adjusted by adjusting the power of the medium frequency power supply. Generally, the pushing is controlled at 950-1020 ℃, and the pushing speed is controlled at 30-100 mm / min.
4. Heat treatment
4.1. For finished pipe fittings, our company carries out heat treatment in strict accordance with the heat treatment system specified in the corresponding standards. Generally, the heat treatment of small pipe fittings can be carried out in resistance furnace, and the heat treatment of large-diameter pipe fittings or elbows can be carried out in fuel oil heat treatment furnace.
4.2. The furnace Hall of the heat treatment furnace shall be clean and free of oil, ash, rust and other metals different from the treatment materials.
4.3. Heat treatment shall be carried out in strict accordance with the heat treatment curve required by the "heat treatment process card", and the temperature rise and fall speed of alloy steel pipe parts shall be controlled to be less than 200 ℃ / hour.
4.4. The automatic recorder records the rise and fall of temperature at any time, and automatically adjusts the temperature and holding time in the furnace according to the predetermined parameters. During the heating process of pipe fittings, the flame shall be blocked with a fire retaining wall to prevent the flame from directly spraying onto the surface of pipe fittings, so as to ensure that the pipe fittings will not be overheated and burned during heat treatment.
4.5. After heat treatment, metallographic examination shall be carried out for alloy pipe fittings one by one. The actual grain size shall not be thicker than grade 4, and the grade difference of pipe fittings of the same heat number shall not exceed grade 2.
4.6. Carry out hardness test on the heat treated pipe fittings to ensure that the hardness value of any part of the pipe fittings does not exceed the range required by the standard.
4.7. After heat treatment of pipe fittings, the oxide scale on the inner and outer surfaces shall be removed by sand blasting until the metallic luster of visible materials. The scratches, pits and other defects on the material surface shall be polished smooth with tools such as grinding wheel. The local thickness of the polished pipe fittings shall not be less than the minimum wall thickness required by the design.
4.8. Fill in the heat treatment record according to the pipe fitting number and identification, and re write the incomplete identification on the surface of the pipe fitting and the flow card.
5. Groove processing
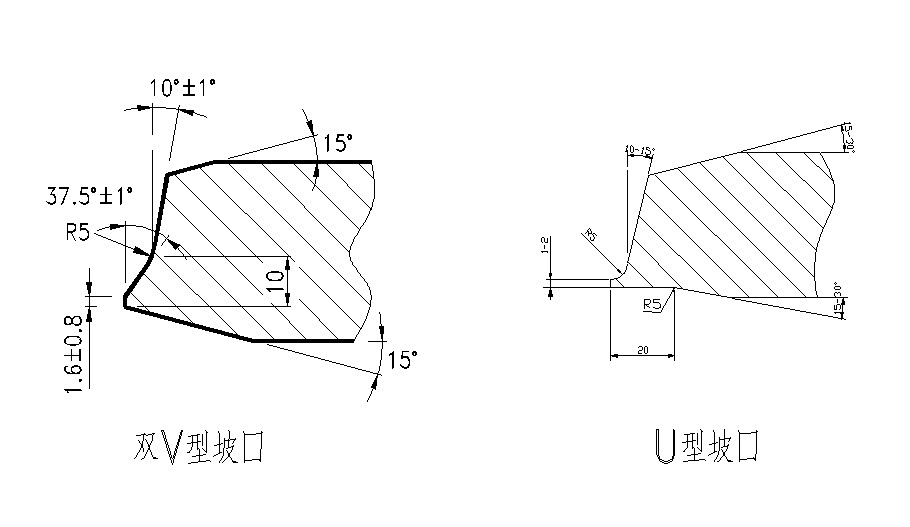
5.1. The groove processing of pipe fittings is carried out by mechanical cutting. Our company has more than 20 sets of machining equipment such as various lathes and power heads, which can process the double V-shaped or U-shaped groove, inner groove and outer groove of various thick wall pipe fittings according to the requirements of our customer. The company can process according to the groove drawing and technical requirements provided by our customer to ensure that the pipe fittings are easy to operate and weld in the welding process.
5.2. After the pipe fitting groove is completed, the inspector shall inspect and accept the overall dimension of the pipe fitting according to the drawing requirements, and rework the products with unqualified geometric dimensions until the products meet the design dimensions.
6. Test
6.1. Pipe fittings shall be tested according to the standard requirements before leaving the factory. According to ASME B31.1. All tests are required to be completed by professional inspectors with corresponding qualifications recognized by the State Bureau of technical supervision.
6.2. Magnetic particle (MT) testing shall be carried out on the outer surface of tee, elbow and reducer, ultrasonic thickness measurement and flaw detection shall be carried out on the outer arc side of elbow, tee shoulder and reducer reducing part, and radiographic flaw detection or ultrasonic flaw detection shall be carried out on the weld of welded pipe fittings. The forged tee or elbow shall be subject to ultrasonic testing on the blank before machining.
6.3. Magnetic particle flaw detection shall be carried out within 100mm of the groove of all pipe fittings to ensure that there are no cracks and other defects caused by cutting.
6.4. Surface quality: the internal and external surfaces of pipe fittings shall be free of cracks, shrinkage cavities, ash, sand sticking, folding, missing welding, double skin and other defects. The surface shall be smooth without sharp scratches. The depression depth shall not exceed 1.5mm. The maximum size of the depression shall not be greater than 5% of the circumference of the pipe and not greater than 40mm. The weld surface shall be free of cracks, pores, craters and splashes, and there shall be no undercut. The internal angle of the tee shall be smooth transition. All pipe fittings shall be subject to 100% surface appearance inspection. Cracks, sharp corners, pits and other defects on the surface of pipe fittings shall be polished with a grinder, and magnetic particle flaw detection shall be carried out at the grinding place until the defects are eliminated. The thickness of pipe fittings after polishing shall not be less than the minimum design thickness.
6.5. The following tests shall also be conducted for pipe fittings with special requirements of customers:
6.5.1. Hydrostatic test
All pipe fittings can be subject to hydrostatic test with the system (the hydrostatic test pressure is 1.5 times of the design pressure, and the time shall not be less than 10 minutes). Under the condition that the quality certificate documents are complete, the ex factory pipe fittings may not be subject to hydrostatic test.
6.5.2. Actual grain size
The actual grain size of finished pipe fittings shall not be thicker than grade 4, and the grade difference of pipe fittings of the same heat number shall not exceed grade 2. The grain size inspection shall be carried out according to the method specified in Yb / t5148-93 (or ASTM E112), and the inspection times shall be once for each heat number + each heat treatment batch.
6.5.3. Microstructure:
The manufacturer shall carry out microstructure inspection and provide microstructure photos in accordance with relevant provisions of GB / t13298-91 (or corresponding international standards), and the inspection times shall be per heat number + size (diameter × Wall thickness) + heat treatment batch once.
7. Packaging and identification
After the pipe fittings are processed, the outer wall shall be coated with antirust paint (at least one layer of primer and one layer of finish paint). The finish paint of carbon steel part shall be gray and the finish paint of alloy part shall be red. The paint shall be uniform without bubbles, wrinkles and peeling. The groove shall be treated with special antirust agent.
Small forged pipe fittings or important pipe fittings are packed in wooden cases, and large pipe fittings are generally naked. The nozzles of all pipe fittings shall be protected firmly with rubber (plastic) rings to protect the pipe fittings from damage. Ensure that the final delivered products are free from any defects such as cracks, scratches, pull marks, double skin, sand sticking, interlayer, slag inclusion and so on.
The pressure, temperature, material, diameter and other pipe fitting specifications of pipe fittings shall be marked on the obvious part of pipe fitting products. The steel seal adopts low stress steel seal.
8. Deliver goods
The qualified transportation mode shall be selected for the delivery of pipe fittings according to the needs of the actual situation. Generally, the domestic pipe fittings are transported by automobile. In the process of automobile transportation, it is required to firmly bind the pipe fittings with the vehicle body with high-strength soft packaging tape. During the driving of the vehicle, it is not allowed to collide and rub with other pipe fittings, and take rain and moisture-proof measures.
HEBEI CANGRUN PIPELINE EQUIPMENT CO.,LTD is a professional manufacturer of pipe fittings, flanges and valves. Our company has an engineering and technical service team with rich engineering experience, excellent professional technology, strong service awareness and fast and convenient response to users all over the world. Our company promises to design, organize procurement, production, inspection and test, packaging, transportation and services in accordance with the requirements of ISO9001 quality management and quality assurance system. There is an old saying in China: It is such a delight to have friends coming from afar.
Welcome our friends to visit the factory.
Post time: May-06-2022